We had set the date of Saturday, March 9, 2019 for the sewing party and I had sent an advance email, requesting volunteers from our museum advisory committee to help sew. The sewing of the Velcro/twill strips does not need to be done by a professional, but it does require care and attention to detail in order that the stitches distribute the weight of the textile evenly, and that the sewing thread runs between the warp and weft yarns rather than piercing any of the textile yarns. On the Friday before our sewing party, Tawney and I set out four textiles and the sewing supplies: tapestry needles, colored thread, scissors, and the corresponding Velcro/twill strips.
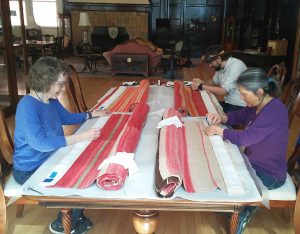
Sewing Velcro/twill strips to textiles at the Luther Bean Museum
On Saturday morning, four of us met at the Luther Bean Museum for our sewing party: Tawney Becker, Linda Relyea, Delfin Weis, and me. We worked around the very long dining table that serves as our conference table in the museum. I showed each person how to place the Velcro/twill strip along the end of the textile and how to sew the strip onto the textile. Also, and very importantly, how to avoid piercing the textile threads, which means a constant look at where the tip of the needle is coming through the textile on each side of the textile. For the sewing novices like me, it is a slow sewing process. Linda, with sewing experience, was the star! In the three hours that we sewed that morning, we greatly advanced this part of the project. Tawney and I finished sewing the strips to the textiles over the following weeks.