As part of my visit with Carmela Quinto, Curator of Collections at the Millicent Rogers Museum (MRM) in Taos, NM, we looked at some of the methods used to display textiles. After ascertaining that the textile is suitable for mounting or hanging, an appropriate display location is chosen to avoid exposing the textile to UV light or other possible damage.
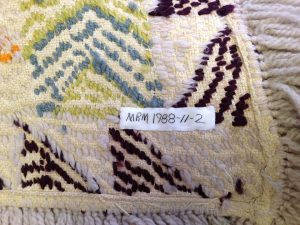
Accession number on textile at MRM
While textiles may be temporarily identified with an acid-free paper tag, the permanent means of identification is to sew a strip of cotton muslin with the accession number marked in permanent ink onto the back of the textile. Archival markers are available for this purpose.
Weft-faced textiles such as Rio Grande textiles, are hung with the warp threads in the vertical position to give the best support to the textile.
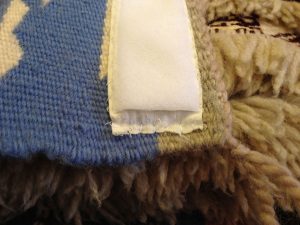
Velcro strip attached to back of textile at MRM
One method to hang textiles for display uses Velcro strips. A strip of Velcro is sewn onto a slightly larger strip of cotton twill or muslin, which in turn is sewn onto the back of the textile at its vertical top end. Small textiles may have two short strips. Larger textiles have one strip that is the width of the textile. Very large or heavy textiles may have a number of strips, each the width of the textile, and at varying distances along the vertical dimension. The other side of the Velcro is attached to sealed or varnished wood strips that are affixed to the display wall.
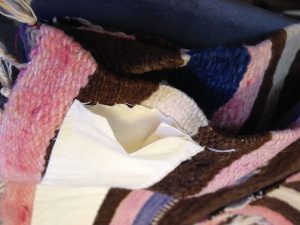
Sleeve attached to the back of textile at MRM
Another method to hang textiles for display uses sleeves. Cotton muslin is cut to the width of the textile and sewn into a hollow sleeve. The sleeve is then sewn onto the back of the textile at its vertical top end, leaving the sleeve ends open. The sleeve can then accommodate either a flat metal bar or a varnished wooden dowel.
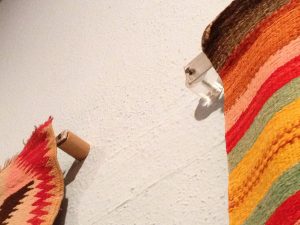
Textiles hung with flat metal bars at MRM
At left, flat metal bars work well with the spacers which are used to create an airspace between the textile and the display wall. Below, a wood dowel through the sleeve, with eye screws at each end, works well for hanging a textile from the ceiling.
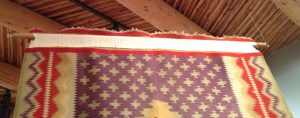
Textile hung with wood dowel at MRM