Lecture by Mark Winter and Chris Ferguson on Pueblo and Navajo Textiles, at the 2018 NMAM Conference, Taos, NM
Immediately following their lecture on Saltillo and Rio Grande blankets, Mark Winter and Chris Ferguson did a second lecture on Pueblo and Navajo textiles. The Luther Bean Museum is home to six Navajo textiles so I was interested to see this lecture and the textile examples that Mark would provide.
Early Pueblo Indians initially used a backstrap loom but around 700 A.D. they converted to a vertical loom using a continuous warp. They farmed cotton for weaving and, after the Spanish introduced sheep to the region, switched to wool. Pueblos produced a woven square cloth called a manta, worn as a shawl or dress. Around 1600, the Navajo picked up weaving skills and adopted the Pueblo upright loom, typically weaving textiles that were wider than they were long. They became very skilled weavers, producing highly prized and expensive textiles, so tightly woven that they had a waterproof quality.
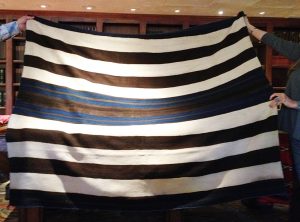
1st Phase Chief Blanket,
courtesy of Mark and Linda Winter
By 1805 the Navajo were already weaving “Chief” blankets in the style referred to as 1st Phase. These had two brown and three white bands at the top and bottom, and two sets of double indigo bands at the center.
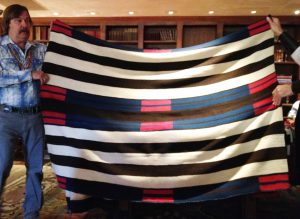
2nd Phase Chief Blanket,
courtesy of Mark and Linda Winter
Navajos valued the red color seen in Mexican serapes, flannels, and other cloth. In raids, they carried off all of the red cloth (bayeta) they found, raveled the yarns, and wove it into their textiles. Traders and trappers carried red cloth for bargaining. This bayeta appears in the 2nd Phase Chief blankets of circa 1855 to 1865. Initially these blankets had twelve sets of red bars within the brown and indigo bands.
Modified 2nd Phase blankets, such as the one modeled by Chris Ferguson in the photograph on the left, incorporated more and more red and were so valued that one blanket was worth ten buffalo robes.
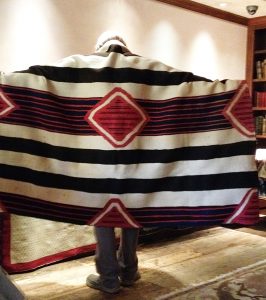
3rd Phase Chief Blanket, courtesy of Mark and Linda Winter
In 3rd Phase Chief’s blankets, red bayeta in the design included nine spots or diamonds and additional red stripes within the indigo bands. Variations of this phase have intricate designs. Mark Winter models the blanket in the photograph on the right.
Designs were conceived as they would appear on the wearer and were held in the mind of the weaver as they were translated into the woven textile.
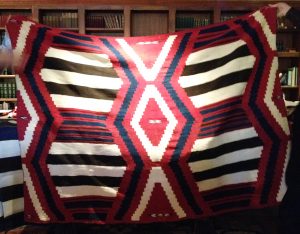
4th Phase Chief Blanket, courtesy of Mark and Linda Winter
By 1865 to 1875, the diamonds had grown so large that they had coalesced in the 4th Phase Chief blankets. In variants of this phase the diamonds became crosses, and after 1860, aniline (synthetic) dyes were incorporated as well.
In addition to the Chief blankets, other Navajo textiles included: serapes (blankets) with red bayeta, and indigo stripes on a large field of natural white, and Navajo versions of Mexican Saltillos with intricate designs on large red fields. Navajo blankets were in high demand after the 1821 opening of the Santa Fe Trail, and remained so later, with the coming of the trains in the 1880s, for the tourist trade.